Dispensing of fluid materials is one of the core technologies in micro assembly industry. Dispensing techniques range from dispensing of adhesive dots over dispensing of solder paste on eletrical contact pads to conformal coating for sealing complete surfaces. The applications are very different – but all need to be very precise.
Precision in this context means to dispense a defined amount of the material. In micro systems production the required amounts of dispensed material can be in the nano liter range (1nl = 1×10-9l) and below. The used dispensing technology has to ensure that these parameters have to be reached – indepentently of varying material properties or environmental effects. Furthermore the required process stability and process capability, that are necessary to ensure a constant product quality are another challenge. This is a functional requirement as insufficient precision and reproducability affect the product.
The requirements of precision and reproducability are relevant for the following parameters:
- volume V=f(x,y,z)
- position (x,y)
- contour accuracy (eccentricity of circles, straightness of lines, shape of points, etc.)
Further important values in terms of processing dispensing materials are:
- density ρ
- viscosity η
- fillers
- surface tension σ
- thixotropy for filled materials (SMD adhesives, solder paste, etc.)
- curing process of adhesives (UV-curing, thermal curing, etc.)
Not all of this information is always published by the dispensing material manufacturers in technical data sheets or safety data sheets. Due to the variety of dispensing materials and dispensing technologies as well as the lack of important material parameters, it is usually necessary to carry out appropriate dispensing tests. This is also caused by a multitude of influences on the material and the stochastic fluid dynamics.
In micro assembly production dispensing processes are often combined with a pick & place process. Common dispensing materials are adhesives, lacquers or solder paste. Each different material requires a corresponding process. For instance, a UV-curing adhesive initially needs to be activated with appropriate UV radiation or cured in the middle of the assembly process or afterwards. The soldering process usually follows the upstream dispensing and assembly process. Depending on the requirements, the soldering process can be carried out as reflow soldering or laser soldering.
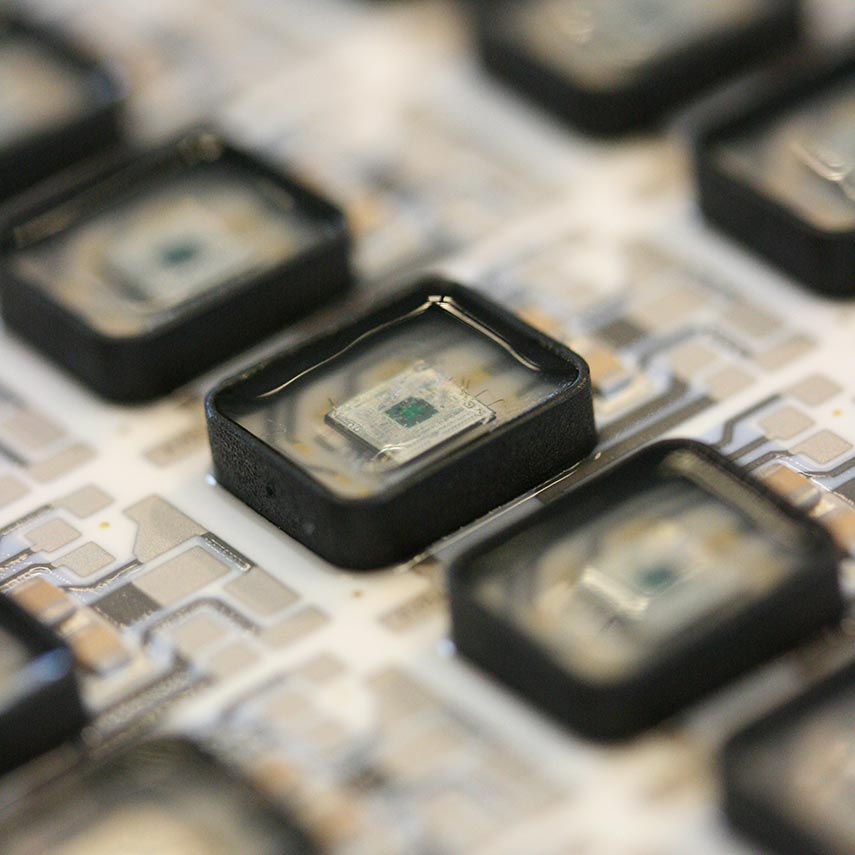
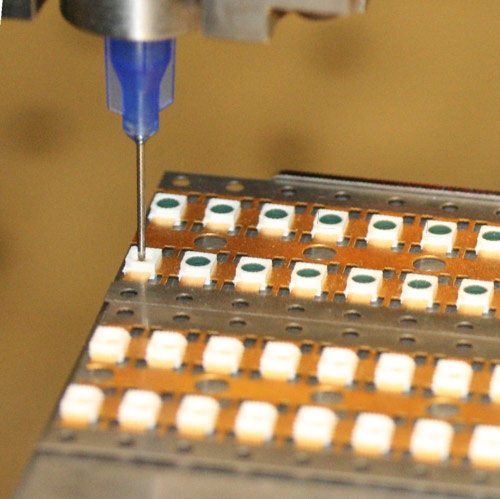
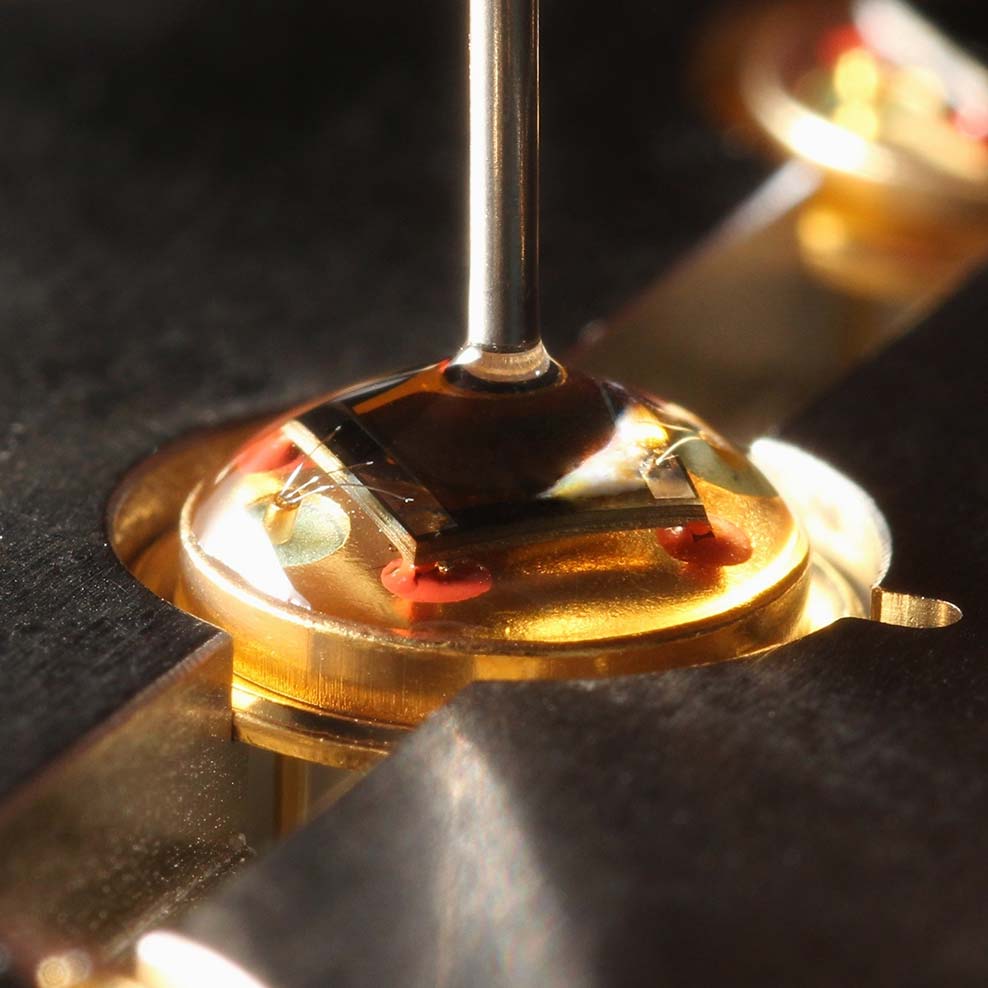