Technological requirements for direct dispensing
The following statements and their detailed explanations should facilitate the selection of suitable dispensing materials. The dispensing materials are referred below as substance. As the properties of the materials have a high degree of variety and even fluctuate greatly, the specified properties and values are to be understood as guideline values.
The substance must allow processing with a squeegee.
The substance must allow appropriate layer thicknesses. The layer thickness must be adjustable and generated homogeneously. Particle sizes, shapes and materials are most responsible for the processability with a squeegee. For instance, if the materials are too soft, there is a risk of clumping. For very small layers only monodisperse materials are suitable. A suitable substance guaratees a constant refilling of the squeegee from the reservior. Furthermore, it forms a cylinder shape behind the squeegee.
The processing time must match the potlife.
Regarding the degeneration of the material, it should be noted that the substance is exposed to air and constantly “rolled” during the coating process. Evaporating substances should be used with care and the material components should not tend to separate (e.g., “bleed”). The substance should not be UV sensitive as it is constantly exposed to light. The application of the coating on the component must be reproducable without stringing or tailing. The substance must maintain sufficient viscosity and wettability throughout the whole manufacturing period.
The component to be wetted must allow direct dispensing.
The component must have sufficient size for a secure fixation at the handling system during substance application. Empirical values are component wetting areas in the range of (x, y) ≥ 0.5mm × 0.5mm. Again, the material properties are a limiting factor. Vice versa, the component must match the dispensing unit (currently (x, y) ≤ 10mm × 10mm) regarding its maximum size. Furthermore, component height, substance height and wetting area on the component should meet the material properties during the coating process. That means the required amount of substance must be applicable to the component.
The wetting form should be reproducible.
It is important to ensure that the wetting structure always produces a defined fluid breakup. In addition, the design of the structure should avoid air inclusions within the coating. Therefore, material should be displaced from the inside to the outside on the wetting area during plunging the component. A confluence of material should be prevented, as this often encloses air within the wetting area. In order to prevent an irreversible deformation of the coating membrane of the dispensing unit, the force during the plunging should be limited. Thus, too small areas, egdes and pins are inapplicable (Edges ≤ 50µm, no single pins). Comparing the contact pressure with the membrane properties should give a first answer. The properties of the membranes can vary due to the fact that these are adjusted to the application (typical membrane from Häcker Automation: Polyethylen (low density); film thickness 30µm±1µm without defects).
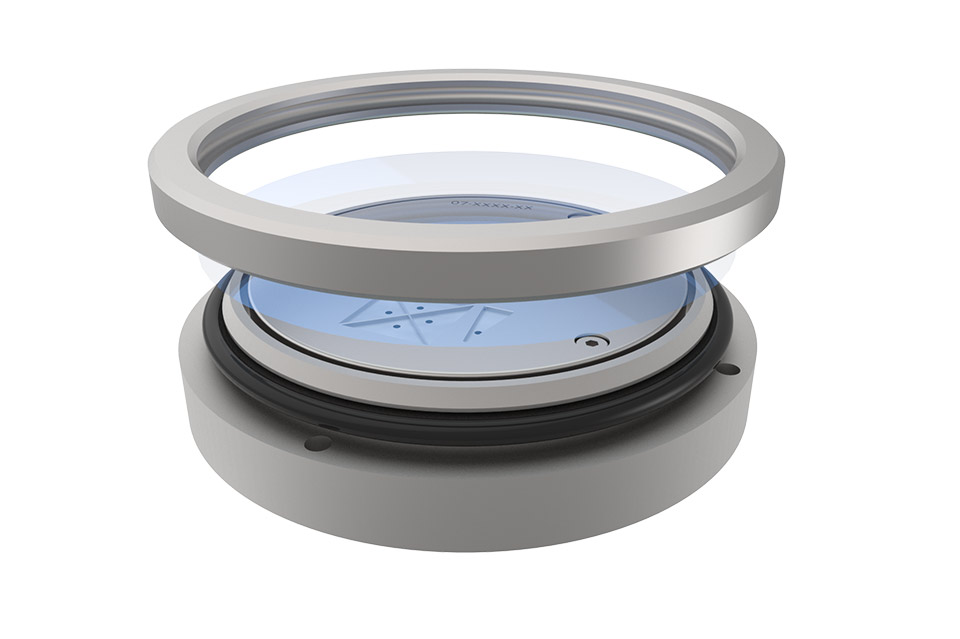